Speed Up Your Service Offerings and Increase Customer Satisfaction Through Effective Service Parts Management
Customers expect fast and efficient service, especially in today’s digital world. If your company can’t keep up, you’ll risk losing customers to your competitors.
But servicing or upgrading an already installed machine years later can be challenging. Over time, spare parts, interfaces, laws and regulations have changed. At the same time, new features and functions have been introduced.
How do manufacturers keep up with both servicing sold products in the field as well as optimize upgrades for greater revenue and customer satisfaction?
In the past, once the sale transaction has been executed, most manufacturers viewed their role in maintaining that product as minimal and reactive.
Product configuration is not only applied when a machine is sold, but also as machines are maintained, repaired and updated.
As time has gone on, and products become increasingly more complex with software and sensors, the connection back to the manufacturer has become stronger. Add to this the advent of ‘product as a service,’ where manufacturers become, once again, owners of the product and merely lease it out based on usage, the shift in both business and operational strategy requires a different approach.
With B2B manufacturers coming full circle, from selling products and equipment to leasing and maintaining them, the need for accurate product configuration data has never been more critical.
For example, service parts management must be able to answer multiple questions quickly and accurately, including:
- How do I upgrade my machine?
- If I change X and Y part, what else do I need to change?
- What is the fastest way to upgrade my machine?
- If I change this component (e.g. electronic controller), will the rest still work?
- If I make this choice what is the impact?
Those manufacturers that have a transparent overview of every product configuration for service and parts for their install base will be able to most efficiently, accurately and profitably provide service and upgrades.
Configuration knowledge can cover all aspects of a machine, including hardware (physical description of machine), software (logical control of the machine) and commercial aspects (how the machine is sold).
Configuration Lifecycle Management (CLM) for Service provides the ability to correctly configure an upgrade for existing products, analyze which parts are no longer compatible, alert for conflicts, and offer suggestions for repair. Powered by Virtual Tabulation® (VT™) technology, CLM for Service enables customers to quickly and accurately configure an upgrade, with the understanding of potential conflicts, why it’s a conflict, and have the transparency needed to make the right choices when building their service parts planning capabilities.
This provides manufacturers / the tools to arm their sales and service personnel with the technology to provide best in class service, options for upgrading, and enhancing and extending a positive customer relationship for greater brand / positive brand experiences.
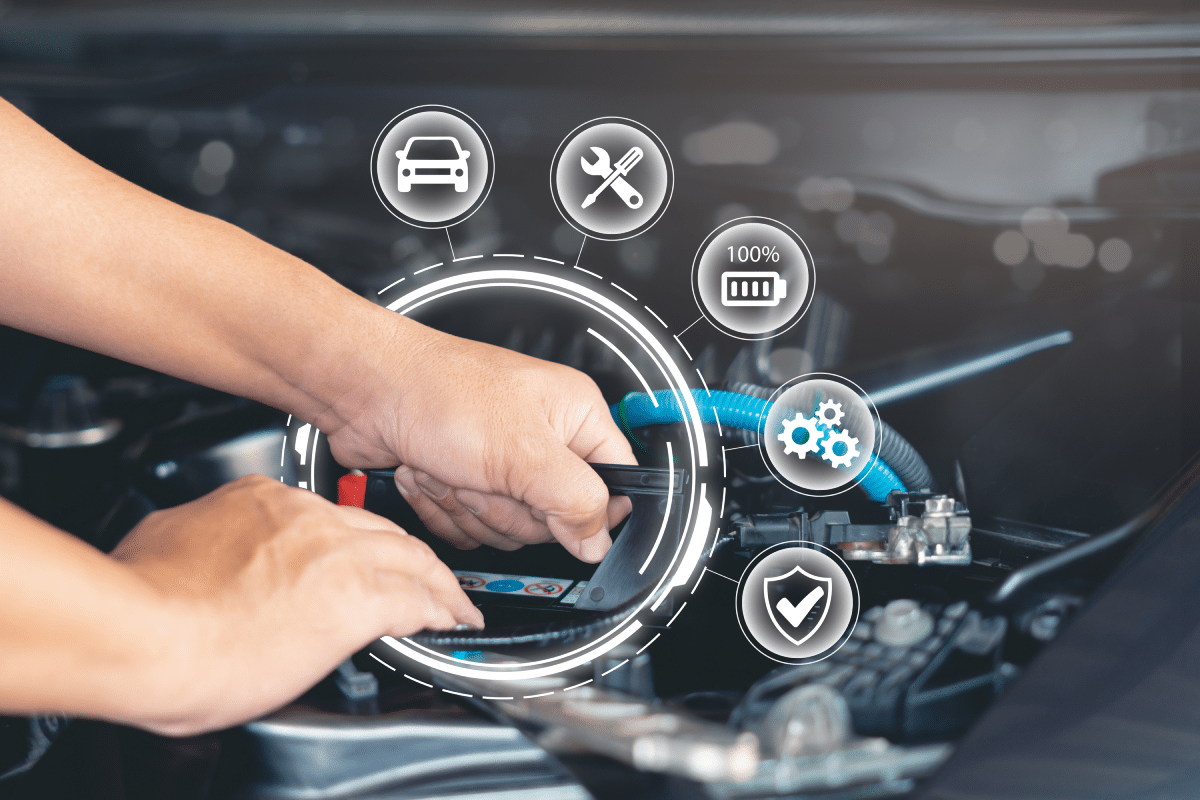
By optimizing service configuration management, manufacturers can:
- Increase revenue-generating opportunities, at better margins
- Reduce risk of invalid updates
- Increase brand loyalty
- Save cost of unplanned service and support efforts
- Enhance customer loyalty
With a single source of shared configuration truth, manufacturers can not only keep track of all installed configurations but leverage this data across the enterprise so that each function associated with the product can have the opportunity to provide fast, efficient service, offer the latest product upgrades, or advise on current and future functionalities.
Effective Service and Predictive Maintenance with a
Single Source of Configuration Truth
About the Author
Henrik Hulgaard, is the Vice President, Product Management and co-founder of Configit, a global Configuration Lifecycle Management (CLM) solution provider and a supplier of business-critical software for configuring complex products. He holds a doctorate in computer science from the University of Washington and is an associate professor of computer science. He has published more than 25 articles internationally.